現在でも鉄系材料がメインだが、自動車における鉄系素材の使用率は、1973年の約80%から実は2001年の時点で約70%に減少(資料:自動車工業会)。高性能を追求するハイスペックなモデルでは、軽量化を目的に外装や機関系を中心にアルミニウムなどへの置換が進み、ホンダ・NSX(1990年)やジャガー・XJ(2003年)でオールアルミボディが採用されたことは広く知られるところ。今ではエンジンにもアルミ製シリンダーブロックが広く普及している。
さらに現在では、環境への配慮や低燃費性能へのニーズの急速な高まりを受け、こうした軽量化を図るための鉄系素材の代替が一層加速している。そして、内外装ともに注目が集まっているのが、FRP(繊維強化プラスチック)を含めた樹脂素材だ。
◆新素材開発にしのぎを削る素材メーカー各社
5月22~24日に開催された、業界第一線の技術者・研究者向けの展示会「人とくるまのテクノロジー展2019横浜(主催:自動車技術展)」では、すでに実用化された製品から将来クルマに使われるかもしれない新たな開発品まで多数の樹脂素材が展示され、樹脂を活用した多様な未来の自動車像が示されていた。
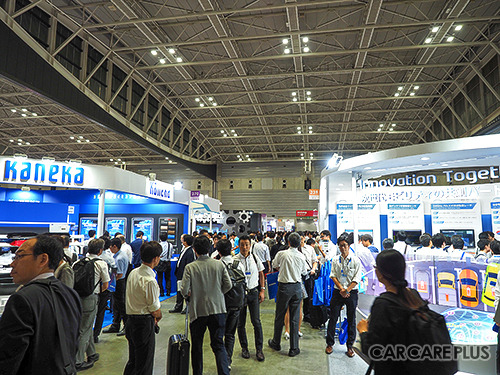
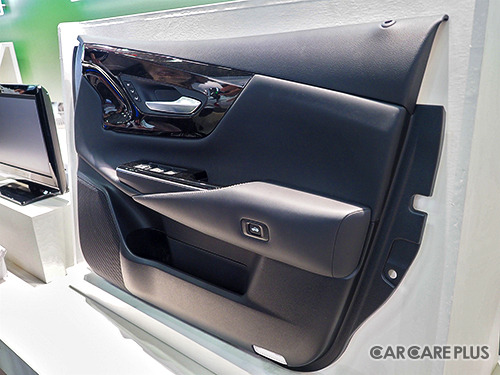
例えば、自動車技術会が「技術開発賞」を授賞したのがトヨタ紡織の高耐衝撃軽量発砲ドアトリム。世界トップレベルという優れた耐衝撃性能を持つプラスチックを活用した技術で、高い衝撃性能を維持したまま従来比で約20%の軽量化を実現。昨年クラウンにすでに導入されている。
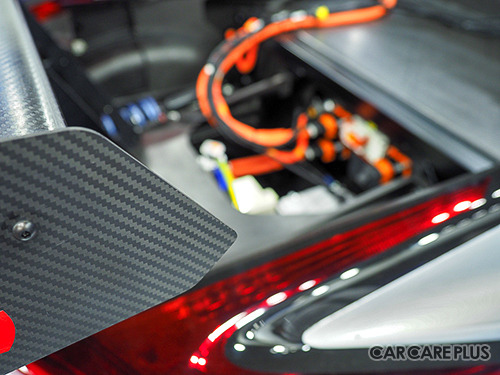
軽量・高強度な樹脂パーツといえば、昔からクルマ好きの間では“カーボン”の呼び名で知られるCFRP(炭素繊維強化樹脂)も進化が目まぐるしい。高コストゆえにレーシングカーやチューニングパーツなど、その用途は極めて限られていたが、電気自動車や量産車へもじわりと広がりつつある。
東レのブースでは、モノコックやサブフレーム、ルーフをCFRP化した日産・リーフNISMO RCを展示。日産・GT-Rのトランクリッドやトヨタ・プリウス PHVのバックドアなど、すでにCFRPを用いたパーツを実用化する三菱ケミカルのブースでは、レクサス・LC500のドアインナーや現代・ジェネシスG70スポーツのトランクリッドなども展示されていた。
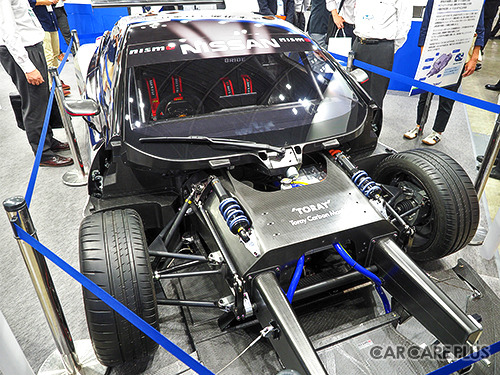
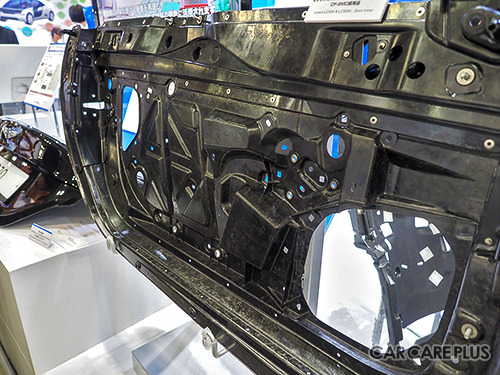
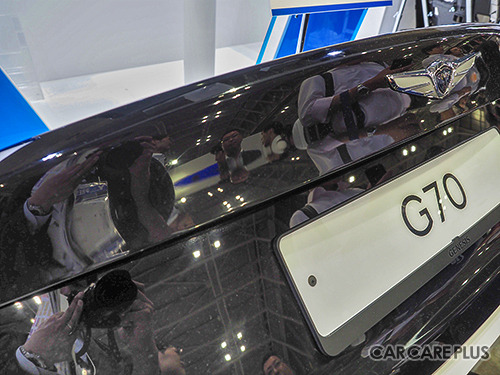
また、CFRPよりもコストが抑えられるGFRP(ガラス繊維強化樹脂)も開発が盛んだ。帝人グループでは、ガラス繊維に含浸させた熱硬化性樹脂を活用したバックドアフレームや外装パネルを展示。実際に導入している例としてBMW・i8ロードスターの外装パネルでは、鉄比で40%、アルミ比で5%の軽量化を実現しているという。
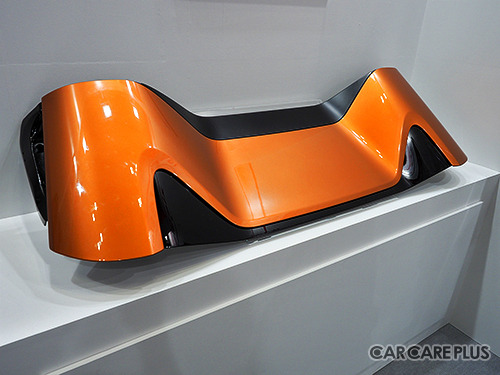
さらに旭化成のブースには、CFRPとGFRPを組み合わせ、表層にガラス繊維強化ポリアミド樹脂を、本体には炭素繊維強化樹脂を組み合わせたホイールを展示。あくまで実用前段階の参考出品だが、鉄チンよりも軽量とされるアルミホイールに比べ、同サイズの場合で約40%軽量化することが可能だそうだ。
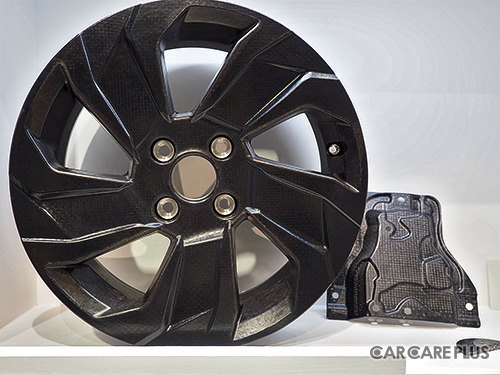
展示品には実用前の参考出展も多く、自動車用素材として実際に採用されるためには耐久性や強度、安全性、コストなどさまざまな要件をクリアする必要がある。素材ごとに性質上得意、不得意もあるため、もちろん次世代の自動車素材=樹脂一択という訳ではない。
それでも、厳しくなる環境規制を背景に、内外装問わずクルマのあらゆるパーツに樹脂を活用すべく、素材メーカー各社が開発にしのぎを削っている。
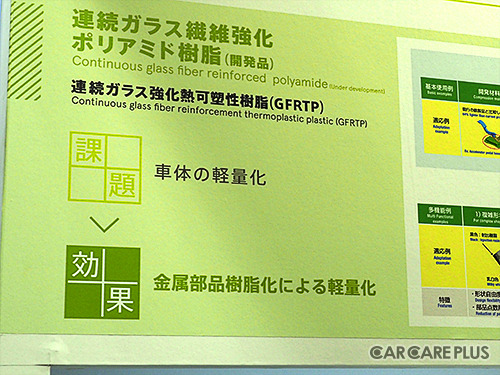
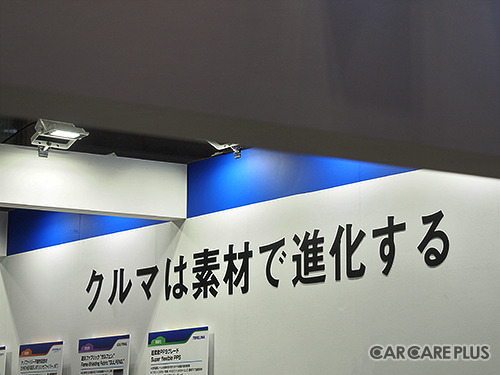
かつては内装などに多く使われ、「安っぽい」「プラスチッキー」などとマイナスな印象を口にされることも少なくなかった樹脂。もしかしたらその樹脂が、そう遠くない将来に “自動車=鉄の塊”の図式を変えるかもしれない。